Corporate Social Responsibility Award
《Managers Magazine》2012 June Issue No. 91
In the past 30 years, due to technology constraints, machine manufacturers use conventional motor with vane pump that are 100% turning all the time no matter what machine movement it is.
Take shoe outsole injection for example, depending on the parts or sizes of outsoles, it’s unnecessary to have the power motor turns in full speed. Or when machine operator is readying uppers on dummy last, the power motor doesn’t need to be operating. A power system that always turning causes hydraulic fluid and motor temperature to be overheated, and reduces injection precision resulting in product defects.
MINZ Inc. managing director Mike Chang noticed high technology industry such as automobile and electric portable devices industry machinery has ample of resources from government funding and corporate investment to maturate plastic injection machines’ power system. “Can we implement the same technology to shoe machinery?” he asked himself.
In 2011, Chang set up an Energy Division, and through agentship of the next generation plastic injection machines, MINZ Energy Division started to learn and transfer this technology to be used in other industrial machines.
MINZ Energy Division approached world renowned shoe manufacturing giant Bata Group for an opportunity of co-developing the first energy system for shoe machinery. Bata Group also was seeking a way to reduce production cost and agreed to allot one production line in Bata’s Indonesia factory for MINZ Energy Division to try.
After installing next generation plastic injection machines’ power system technology to shoe machinery, MINZ team found out it’s not workable because they hydraulic designs are completely different. Shoe machines have many micro movements that far exceed plastic injection machines. Chang leaded his team traveling back and forth Taiwan and Indonesia to make modification to the power saving system. They worked during night time so the modification not affecting Bata’s production schedule in day time hours. After 3 major modifications and researching fund investing, in September 2011, their team finally successfully developed the first power saving system for shoe machinery, and saved 65% of Bata’s shoe production machinery. Besides electricity savings of the machines, hydraulic fluid temperature is now kept at room temperature without the need of chillers. The injection precision is increased also for less shoe defects. “When we saw the electricity recording result of 65% savings, we were all shocked and knew every hard effort we put in is all worth it” said by Chang with smile.
Until today, MINZ Energy System has been installed in different industrial factories in 20 countries around the world and saved more than 170,000 kwh consumption. MINZ has indeed changed these industries’ power usage through their own hands.
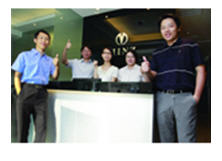
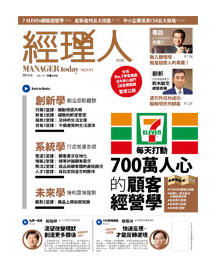