MINZ has been selected as top smart factory solution providers in APAC.
Smart factories setup is speeding up as the COVID pandemic is restricting experts, buyers, and owners from traveling to factories abroad. That’s why factories are now investing in automation and digitalization equipment and tools. But there lies a peculiar challenge. A smart factory has a higher space utilization rate, which leads to less space being provided for the machines. For example, in the shoe industry, PPM (pairs per m²) is emphasized along with PPH (pairs per person) for factory performance measures.
Enter Minz. The company’s smart cutting and IoT solutions can effectively mitigate PPM and PPH by increasing production output and OEE rate of each smart cutting machine using less factory space and reducing both direct and indirect manpower.
On the Smart Cutting side, MINZ is the only manufacturer in APAC that produces both die-less cutting and stroke cutting smart cutting machines suitable for R&D and mass production purposes. “Factory managers can digitally dispatch cutting tasks from ERP/MES remotely to any MINZ auto cutting machines in factory. Production data are then synchronized back to IoT platform and ERP/MES,” says Mike Chang, the General Manager of MINZ.
This real-time productivity data help factory managers control material inventory and WIP (works-in-process). Renowned OEM factories in APAC producing for Nike, Adidas, Puma, and VF have implemented MINZ smart cutting machines CutBot in their smart factories to replace conventional process while ensuring higher productivity, efficiency/space utilization, and more consistent quality to support production and sustainability KPI.
On the IoT front, MINZ Smart Box can be installed on a factory’s existing machines (even if machines are of different brands/models or analog signal outputs) to collect quality-related data such as pressure, temperature, speed, vibration, energy consumption, carbon emission and then digitally compile these data onto one IoT platform.
Whenever machine settings are not within standards range, the IoT platform will trigger the Andon system and alert the factory manager automatically. These production resumes can be traced and analyzed for constant improvements. “Although MINZ Smart Box is shoe-machine-specific, they can be used on other industrial machines with tailor-made functions as shoe machines come in variety of types and data,” mentions Mr. Chang. MINZ has completed the setup of more than 18 assembly lines in smart factories producing Nike, New Balance, and Brooks and providing factory and QC managers real-time monitoring of production floor. Before implementation, managers used to rely on paper recorded data, which is time-consuming and lacks authenticity. Real-time data from the factory floor provides managers actual facts for prompt management even when they are remotely in the office.
Apart from a splendid solution portfolio, MINZ is composed of a team of hydraulic, electrical, mechanical, and IT backgrounds. “Unlike other smart factory solution providers, we design and make both software and hardware and also conduct the installation all by ourselves through service branches located in Indonesia, Vietnam, and Cambodia,” says Mr. Chang. In the following few years, MINZ forecasts an expansion of the 5G network infrastructure in APAC. With 5G’s characteristics of fast data transmitting speed and high coverage rate for multiple signals. It will enable many possibilities for smart cutting and IoT to link with AI (artificial intelligence). Therefore, MINZ has begun developing AI for smart cutting and IoT.
"FACTORY MANAGERS CAN DIGITALLY DISPATCH CUTTING TASKS FROM ERP/MES REMOTELY TO ANY MINZ AUTO CUTTING MACHINES IN FACTORY. PRODUCTION DATA ARE THEN SYNCHRONIZED BACK TO IOT PLATFORM AND ERP/MES"
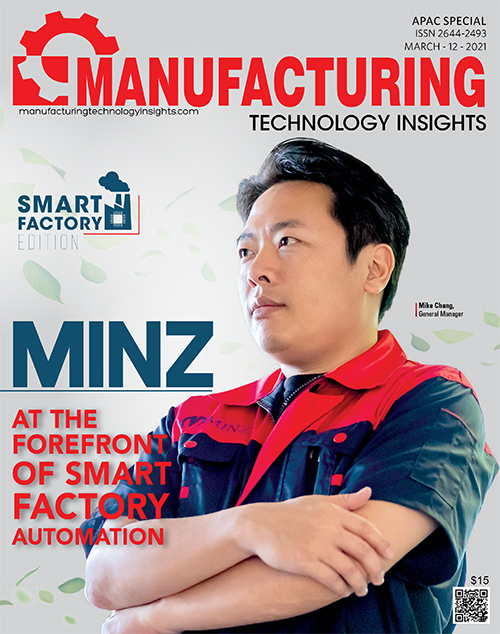
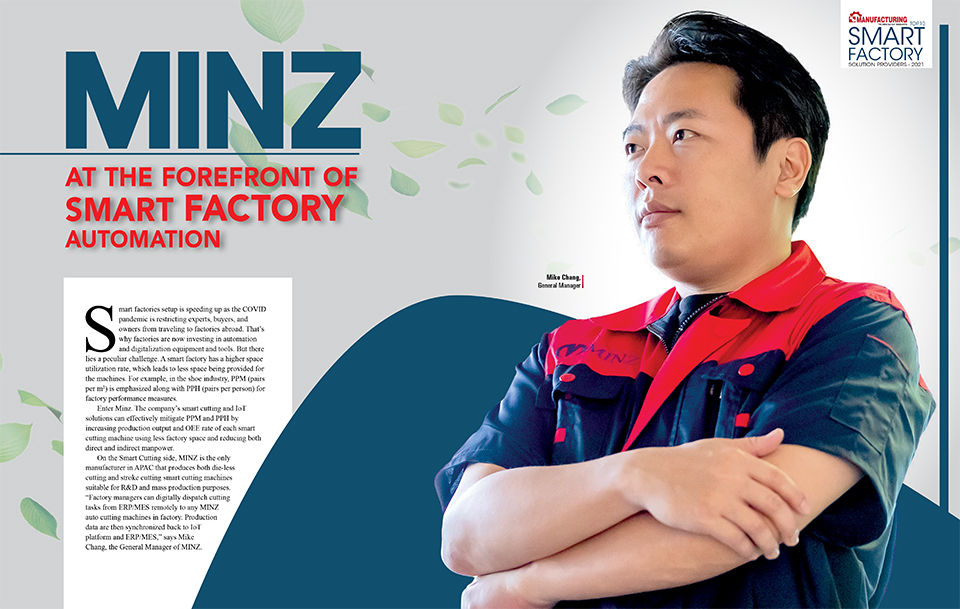
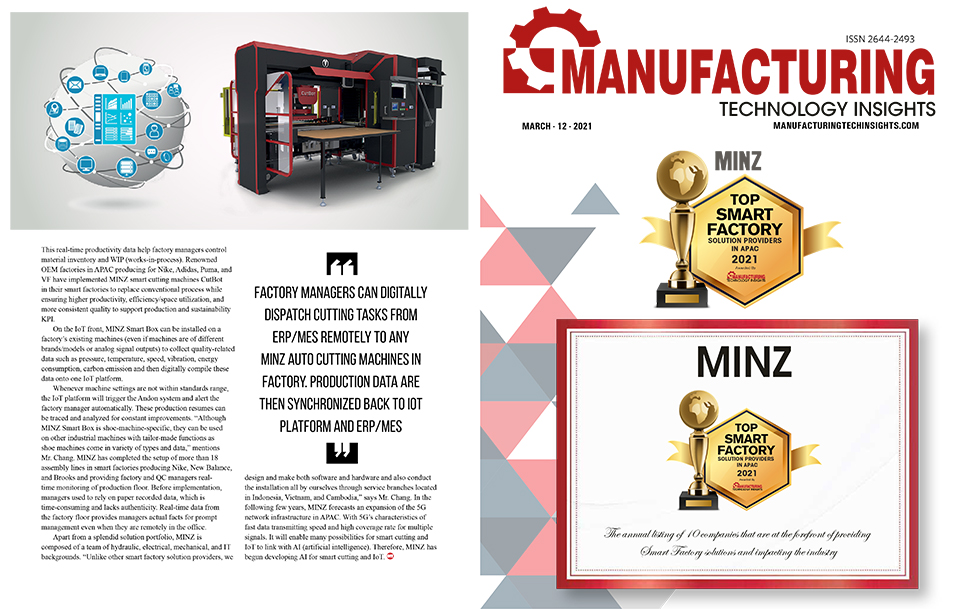